Introduction
Globally, the population of people over the age of 65 is expected to rapidly increase from 524 million in 2010 to nearly 1.5 billion in 2050. Rapid aging is accompanied by degenerative diseases, such as sarcopenia, which is characterized by a reduction in muscle mass and strength (Liao et al., 2019; Park et al., 2021). Dietary protein supplementation is important for preventing muscle loss, and milk proteins are widely used because of their functional, nutritional, and sensorial properties. In particular, whey protein is well known as an effective stimulant for promoting muscle protein synthesis because it is rapidly digestible and contains all essential amino acids and branch-chain amino acids (Gilmartin et al., 2020; Kobayashi et al., 2016). Englund et al. (2017) found that whey protein supplementation (20 g) for six months in 78.5±5.4 years old elderly people could promote an increase in muscle density, compared to the control group. Mori and Tokuda (2018) also reported a positive effect of whey protein supplementation (22.3 g) with exercise on muscle mass in women aged 65–80 years. Therefore, high-protein supplements are a growing market with a drastic increase in the elderly population, and milk proteins can be used as ideal ingredients for sarcopenia prevention.
Dairy-based powder products are required for instant properties related to rapid dispersion without the formation of lumps. However, spray-dried milk proteins have poor flowability and wettability because of their fine particle size and high inter-particle cohesive forces, resulting in slow reconstitution and lump formation problems (Atalar and Yazici, 2019; Ji et al., 2017). The fluidized bed agglomeration process can be used to solve these problems to help produce instant food powder. Fluidized bed agglomeration is defined as the size enlargement from small fine particles to large porous particles, and it can improve physical properties, such as size distribution, flowability, mixing capacity, and dispersibility (Atalar and Yazici, 2021; Park and Yoo, 2020). Currently, protein-fortified milk powders are consumed in Korea to prevent sarcopenia. The demand for high-protein powder products is continuously increasing in the Korean market, and most of these products are manufactured by the dry blending method that simply blends dairy powders, protein powders and other powdered ingredients such as vitamins and minerals (Jang and Oh, 2021; Kang et al., 2020). Some researchers have studied the effects of the fluidized bed agglomeration process on dairy powders such as skim milk powder (SMP; Turchiuli et al., 2013), milk protein isolate (MPI; Ji et al., 2015; Wu et al., 2020), and whey protein isolate (WPI; Ji et al., 2017). However, the effect of the fluidized bed agglomeration process in mixed systems of SMP and milk protein has not yet been studied. Thus, in this study, the improved rheological and physical properties of WPI-fortified SMP produced by a fluidized bed process were investigated, and the influence of the SMP/WPI ratio on fluidized bed agglomeration was also examined.
Materials and Methods
SMP (37% protein and 49% lactose) was supplied by the Seoul Dairy Cooperative (Ansan, Korea), and WPI (HilmarTM 9410, 89% protein and 0.1% lactose) was obtained from Hilmar Ingredients (CA, USA). The SMP was mixed with WPI at ratios of 9:1 (SMP9/WPI1), 8:2 (SMP8/WPI2), and 7:3 (SMP7/WPI3) to manufacture agglomerated WPI-fortified SMP samples.
The fluidized bed agglomeration process was performed according to the method of Barkouti et al. (2013) with slight modification. One kilogram of raw powder was poured into a conical product vessel, and agglomeration of milk powder was conducted using a fluid bed granulator (Fluid Bed Lap System, Einsystem, Anyang, Korea). The temperature of the injected air was set to 95±1°C, and the product temperature in the vessel was maintained at 55±1°C. Distilled water was used as the binder solution, which was pumped at a flow rate of 10 mL/min and sprayed using a fluid spray nozzle at a pressure of 1.5 bar. After spraying with distilled water for 30 min, the agglomerated milk powder was dried using hot air (55°C) for 10 min. The SMP without WPI also agglomerated under the same conditions and was used as the control sample.
The size distributions of the raw and agglomerated WPI-fortified SMP particles were measured using a laser diffraction particle size analyzer (Mastersizer 3000, Malvern Instruments, Worcestershire, UK). The D[3,2] (surface-weighted mean) and span (dispersion index) values were used to determine the size distribution of the agglomerated WPI-fortified SMP particles and were calculated from Eqs. (1) and (2), respectively:
where di is the average diameter of the i class interval, and ni is the number of particles with diameter di. Dv10, Dv50, and Dv90 are the average particle sizes at 10%, 50%, and 90% of the cumulative size distribution, respectively.
The microstructure of raw and agglomerated milk powders was investigated using SEM (Genesis-1000, EmCrafts, Seoul, Korea). Powder samples were attached to SEM stubs using double-sided adhesive carbon tape and coated with gold under vacuum prior to observation. SEM analysis was performed at an accelerating voltage of 20 kV and 200× magnification.
The flowability and cohesiveness of the WPI-fortified SMP particles were measured using the Carr index (CI) and Hausner ratio (HR), respectively, which were calculated using the bulk density (ρbulk) and tapped density (ρtapped). ρbulk and ρtapped were calculated as the mass/volume ratio of the powder samples before and after 1,250 taps, respectively, using a tap density volumeter (BT-301, Bettersize Instrument, Dandong, China), and CI and HR values were calculated from Eqs. (3) and (4):
Powder flowability (%) based on the CI value was classified as follows: <15 very good, 15–20 good, 20–35 fair, 35–45 bad, and >45 very bad. Powder cohesiveness based on the HR value is classified follows: <1.2 low, 1.2–1.4 intermediate, >1.4 high (Atalar and Yazici, 2018; Szulc and Lenart, 2013).
The wetting time (tw) was used to evaluate the hydration properties of raw and agglomerated WPI-fortified SMP particles. As described by Atalar and Yazici (2018), the required time to complete wetting and immersion of 5 g powders in 100 mL distilled water (23±1°C) was measured as the wetting time.
Color analysis of the raw and agglomerated WPI-fortified SMP samples was performed using a “Colorflex” colorimeter (Hunter Associates Laboratory, Reston, VA, USA), which was calibrated using a standard white tile (x=80.32; y=85.18; z=89.28) before measurement. The results were described using EasyMatchQC ver 4.77 software in terms of L* (lightness index) ranging from 0 (dark) to+100 (light), a* (redness index) ranging from –60 (green) to +60 (red), and b* (yellowness index) ranging from –60 (blue) to +60 (yellow), according to the international color system.
Agglomerated milk powder (60 g) was dissolved in 180 mL of drinking water to investigate the rheological properties of the rehydrated milk beverages. Rheological measurements were performed using a HAKKE Roto Visco-1 (Thermo Fisher Scientific, Waltham, MA, USA) equipped with a cone-plate geometry, and data were obtained at a shear rate range of 0.4 to 100 s–1. The data were fitted to the following power-law model to describe the flow behavior of rehydrated solutions:
where σ is the shear stress (Pa), is the shear rate (s–1), K is the consistency index, and n is the flow behavior index. The apparent viscosity (ηa,10) of the sample was calculated at 10 s–1 using the K and n values obtained from the power-law model.
All experiments were conducted in triplicates, and data are expressed as the mean±SD. Statistical analysis was performed using one-way ANOVA, followed by Tukey’s test using the IBM SPSS Statistics 24 software suite (IBM, Armonk, NY, USA). The significance level was set at p<0.05.
Results and Discussion
Particle size and distribution are important characteristics of food powders and can be closely linked to other physical properties, such as density, flowability, and reconstitution. The particle size distribution profiles of the raw and agglomerated WPI-fortified SMP samples are presented in Fig. 1, which shows that the particle size distribution of raw SMP and WPI-fortified SMP samples moved to the large size region as they agglomerated. These results indicate that the particle size of the powders was increased by the fluidized bed process. In principle, fluidized bed agglomeration is performed by spraying the binder solution onto the powders flowing upward by airflow. This process consists of three steps: 1) wetting, 2) coalescence, and 3) consolidation (Atalar and Yazici, 2021; Lim et al., 2021). The raw particles are fluidized by rising hot air, and their surfaces are wetted by a sprayed binder solution, which makes them bind together by the formation of liquid bridges owing to the collision of sticky particles, which then turns liquid bridges into solid bridges, leading to the anchoring of the agglomerated particles (Atalar and Yazici, 2019; Barkouti et al., 2013). Therefore, the fluidized bed process can effectively produce agglomerated milk powder.
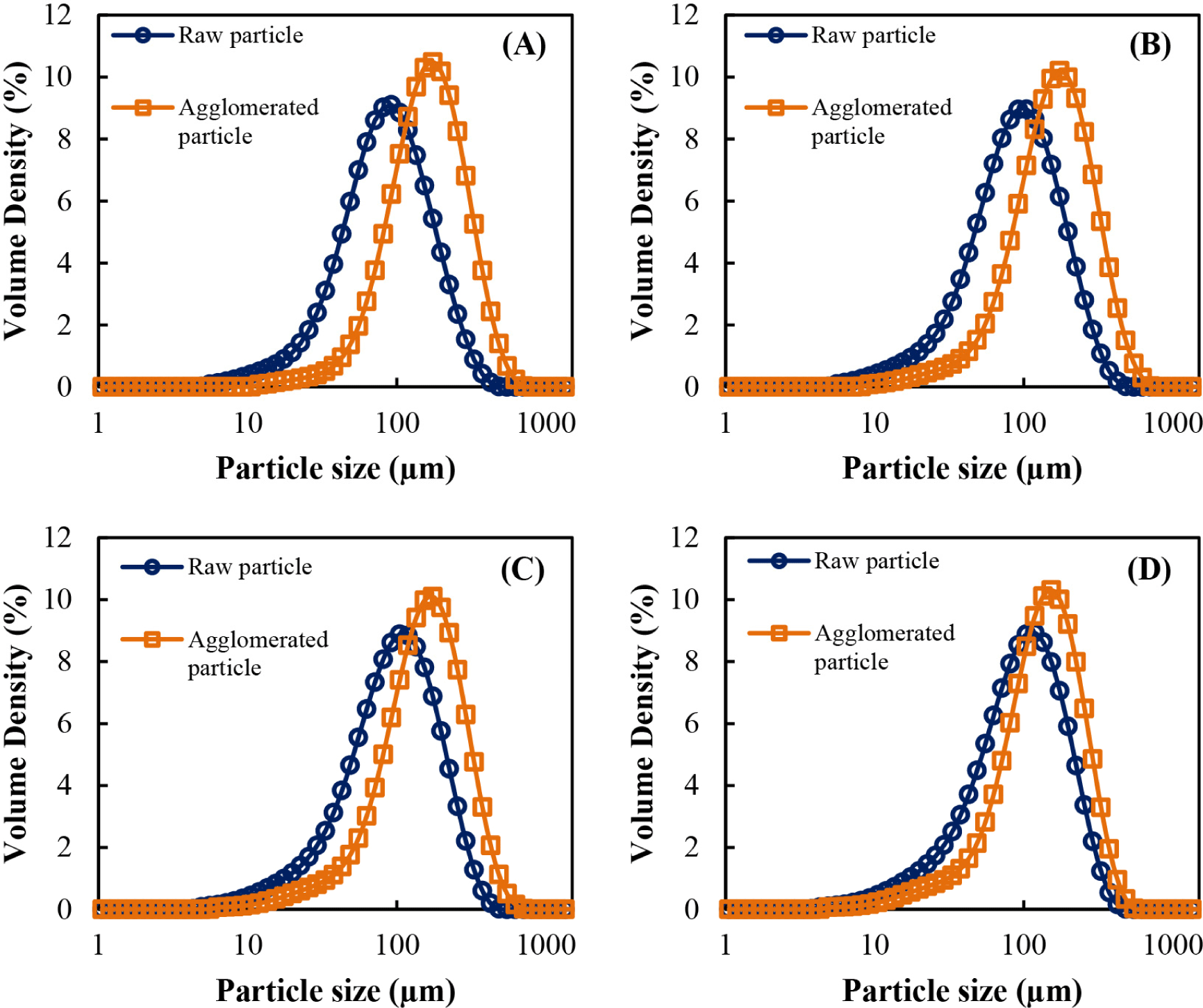
The particle size and distribution values (D[3,2], Dv10, Dv50, Dv90, and span) of the raw and agglomerated WPI-fortified SMP samples are listed in Table 1. The D[3,2] values of raw powders exhibited similar D[3,2] values, which were about 61.6–63.0 μm. But, the D[3,2] values of the agglomerated powders increased in the order SMP7/WPI3 (147%)<SMP8/WPI2 (164%)<SMP9/WPI1 (186%)<SMP (208%), and other particle size values (Dv10, Dv50, and Dv90) also showed a similar tendency. In general, fluidized bed agglomeration is influenced by powder composition, particle size, binder type, and process conditions (Barkouti et al., 2013; Park and Yoo, 2020). In this study, the agglomeration of the WPI-fortified SMP samples may be strongly affected by the powder composition because the fluidized bed agglomeration process was carried out under the same conditions. According to Atalar and Yazici (2019), hydrophilic sugars such as lactose can improve the wettability of food powders, promoting the formation of liquid bridges between particles. Therefore, SMP with high lactose content can be more easily agglomerated by the fluidized bed process than WPI with low lactose content.
One purpose of fluidized bed agglomeration is to achieve a uniform particle size distribution. In general, the span value is used to assess the homogeneity and polydispersity of food powders (Chever et al., 2017). The span values of raw WPI-fortified SMP samples decreased from 2.02 to 1.84 with the increase in WPI ratio. This result can be explained by the increase in Dv50 values, as shown in Table 1. After the fluidized bed process, the span values of the agglomerated SMP and WPI-fortified SMP samples were in the range of 1.58–1.63, and the span values of the agglomerated powders were much lower than those of the raw powders. This reduction in span values indicates a narrow size distribution with homogenous particles. From these results, it was found that WPI enrichment could slightly suppress the agglomeration of SMP by the reduction of liquid bridges between particles due to the decrease in hydrophilic sugar content, but it was concluded that the fluidized bed agglomeration process can effectively improve the particle size distribution.
SEM analysis was used to visualize the microstructures of the SMP and WPI-fortified SMP particles. Fig. 2 shows the SEM images of the raw and agglomerated powders with different structures. The raw SMP (Fig. 2A) and WPI (Fig. 2B) showed small spherical particles, which are typical of milk powders produced by spray dryers (Atalar and Yazici, 2019). Some particles were connected; thus, the particle size distribution was approximately 30–200 mm, consistent with the particle size distribution results shown in Table 1. The fluidized bed agglomeration process had noticeable effects on the size and shape of the SMP and WPI-fortified SMP particles. The SMP was effectively agglomerated by the fluidized bed process, which led to a grape-like structure with high porosity (Fig. 2C). This result can be attributed to the better intermolecular interactions between the SMP particles during the fluidized bed process. Generally, a highly porous structure can improve the reconstitution properties of food powders because it allows water to penetrate easily into the void spaces of agglomerated particles (Ji et al., 2015; Lee and Yoo, 2021; Wu et al., 2020). WPI-fortified SMP particles (Fig. 2D) were partially agglomerated by the fluidized bed process, resulting in the formation of smaller agglomerated particles than agglomerated SMP particles. This result may be due to the lower compatibility between the SMP and WPI particles, which can be explained by the lower wettability of the WPI particles than that of the SMP particles, as described previously. These results suggest that the microstructure of SMP is strongly affected by the fluidized bed agglomeration process and that the enrichment of WPI particles can influence the agglomeration of SMP particles.
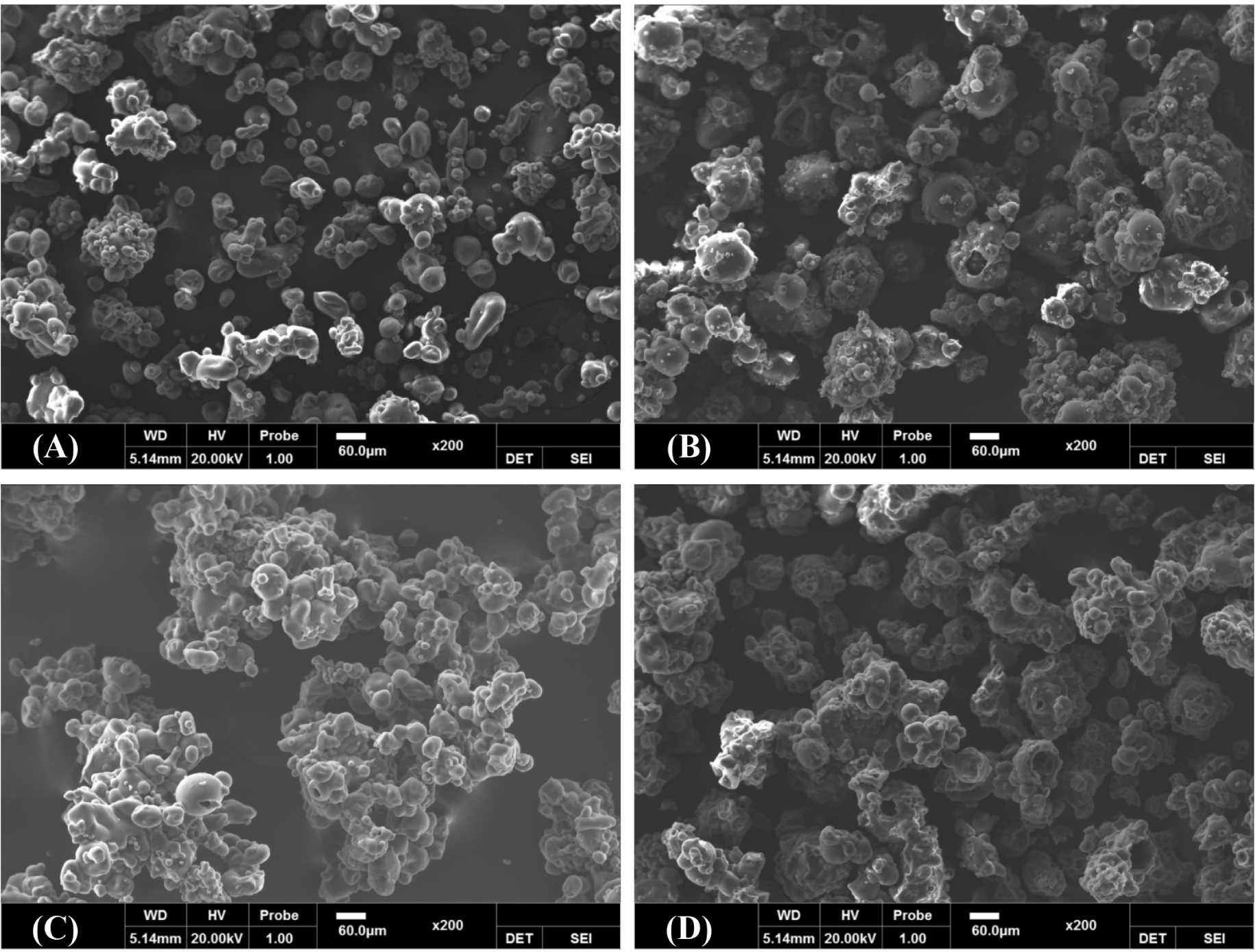
The physical properties of the raw and agglomerated WPI-fortified SMP samples are presented in Table 2. The bulk density (ρbulk) and tapped density (ρtapped) of raw powders were in the range of 0.48–0.64 g/cm3 and 0.63–0.78 g/cm3, respectively, and both ρbulk and ρtapped values decreased to 0.38–0.45 g/cm3 and 0.47–0.51 g/cm3 after fluidized bed agglomeration process, respectively. These results were similar to those by Ji et al. (2017), which reported that WPI powders agglomerated using a lecithin solution as a binder. According to Chever et al. (2017), the fluidized bed process produces a powder with a lower density owing to additional voids caused by the formation of porous structures during the agglomeration process (Ji et al., 2015; Wu et al., 2020). Therefore, the lower ρbulk and ρtapped values of the agglomerated WPI-fortified SMP particles can be attributed to the additional voids within the porous structure of the agglomerated powders by the fluidized bed process.
The ability to flow easily is an important property related to transfer, weighing, storage, and blending (Lee and Yoo, 2021). The flowability and cohesiveness of food powders can be described using the CI and HR, respectively. As shown in Table 2, the CI values of the raw SMP showed good flowability (CI: 15–20) and increased from 18.2 to 22.5 as the WPI ratio increased, indicating fair flowability (CI: 20–25). The HR values of the raw powders exhibited intermediate cohesiveness (HR: 1.2–1.4) and increased with increasing WPI ratio. In contrast, the CI and HR values of the agglomerated powders decreased with increasing WPI ratio, and the CI and HR values of the agglomerated WPI-fortified SMP particles exhibited very good flowability (CI: <15) and low cohesiveness (HR: <1.2). These results indicate that the physical properties of WPI-fortified SMP particles can be improved by the fluidized bed agglomeration process. The improved flowability and cohesiveness of the agglomerated powders can be explained by the increased particle size, which can reduce the particle surface area and decrease friction between the particles (Lim et al., 2021; Park and Yoo, 2020). However, the fluidized bed process did not improve the CI and HR values of the agglomerated SMP samples. This result may be due to the lower ρbulked and ρtapped values of agglomerated SMP particles as compared to the WPI-fortified particles (Lee and Yoo, 2020). From these results, it was suggested that the physical properties of SMP particles are greatly affected by the addition of WPI particles and that the fluidized bed agglomeration process can effectively improve the flowability and cohesiveness of WPI-fortified SMP particles.
Wettability of powders is defined as its ability to overcome surface tension at the interface between liquid and particles, and good wettability is very important for powder products because it is closely related to the hydration properties (Atalar and Yazici, 2018; Ji et al., 2017). The hydration properties of raw and agglomerated WPI-fortified SMP particles were shown in Fig. 3 and Table 2. The raw SMP and WPI-fortified SMP particles had a long wetting time (tw) of >120 s and floated on the water surface with lump formation, as shown in Fig. 3. According to Nascimento et al. (2021), fine particles can penetrate into spaces between large particles and lead to more compact powders. These compact particles do not allow water to penetrate inside the particles, which can form lumps and float on water surface. In contrast, agglomerated SMP and WPI-fortified SMP particles displayed faster wetting, as demonstrated by the decrease in wetting time to 4.33–14.3 s. The same effect was also observed in other studies of isolated protein powders, such as MPI (Wu et al., 2020), pea protein isolate (Nascimento et al., 2021), and soy protein isolate (Machado et al., 2014). This improved wettability can be explained by the large particle size and the porous structure of agglomerated particles. As previously described, the large porous structure can allow water to easily penetrate into the void spaces of agglomerated particles, facilitating the wetting of powders (Custodio et al., 2020; Wu et al., 2020). Although wetting time of agglomerated WPI-fortified SMP particles increased from 4.67 s to 14.3 s with increasing WPI ratio, they showed the faster wetting time than the instant criterion (<20 s) described by Chever et al. (2017). Consequently, the rehydration properties of WPI-fortified SMP particles can be effectively improved by the fluidized bed agglomeration process.
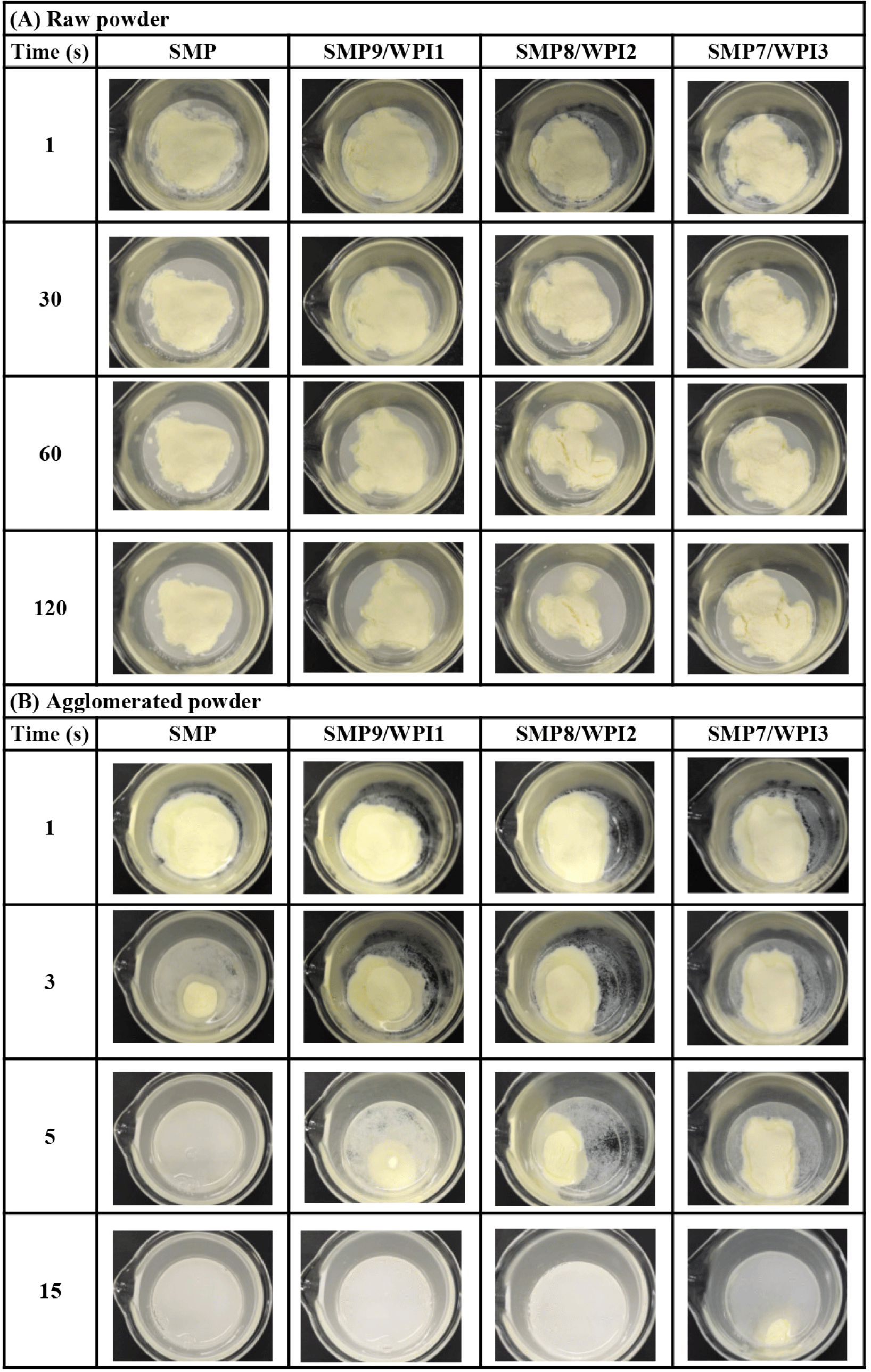
Color is a significant factor in the sensory aspect of food powders, and the changes in the color parameters (L*, a*, and b*) of raw and agglomerated powders are summarized in Table 3. The L* decreased with an increase in the WPI ratio, and the agglomerated powders had lower L* than the raw powders, indicating that the color became darker owing to fluidized bed agglomeration. Similar results were observed by Lee et al. (2021), who reported that the L* of carboxymethyl cellulose powder decreased from 88.3 to 83.7 after fluidized bed agglomeration. This result can be attributed to the increase in particle size. According to Sakhare et al. (2014), larger particle size can decrease the whiteness of food powder. In the case of b*, agglomerated powders have higher values than raw powders, indicating that fluidized bed agglomeration can increase the yellowness of milk powders. The higher b* of agglomerated powders can be explained by the brown pigments produced by the Maillard reaction, which can be accelerated at high temperatures because of hot air (Zulueta et al., 2013). Consequently, the color properties of dairy-based food powders can be influenced by the fluidized bed agglomeration process, which can lead to a decrease in the L* and an increase in the b* owing to the Maillard reaction.
The shear stress (σ) versus shear rate () data were applied to the power law model to describe the flow behavior of rehydrated milk beverages with agglomerated powders, and the experimental results were well fitted to the power law model with high r2 (0.97–0.98), as shown in Table 4. the rehydrated solutions with the SMP and SMP9/WPI1 samples exhibited Newtonian behavior with flow behavior index values of close to 1 (n=0.98–1.02). the n value decreased slightly with increasing WPI ratio, and the rehydrated solution with the SMP7/WPI3 sample showed little shear-thinning behavior (n=0.76). Similar results were reported by Bazinet et al. (2004), who found that the WPI dispersion exhibited shear-thinning behavior above a concentration of 10%. This shear-thinning behavior of the WPI solution can be explained by the breakdown of weak bonds, such as hydrogen and ionic bonds, in the protein network at high shear rates, which can lead to a decrease in viscosity (González-Tello et al., 2009; Tang et al., 1993). the apparent viscosity (ηa,10) and consistency index (K) values of rehydrated solutions were also influenced by the enrichment of WPI and increased with an increase in the WPI ratio. the higher viscosity of the rehydrated solution containing the SMP7/WPI3 sample may be attributed to the higher concentration of protein aggregates. According to Morison and Mackay (2001), the viscosity of whey protein solutions is governed by whey protein and depends on the protein concentration. therefore, these results indicate that the SMP/WPI ratio can influence the flow behavior of rehydrated milk beverages with agglomerated WPI-fortified SMP samples.
Conclusion
the high-protein dairy powder is being consumed to prevent sarcopenia. However, spray-dried milk proteins have poor flowability and wettability owing to their fine particle sizes and high inter-particle cohesive forces. This study aimed to investigate the effect of fluidized bed agglomeration on SMP fortified with WPI with varying SMP/WPI ratios to resolve these problems. the fluidized bed process increased the particle size distribution, and SEM images of the agglomerated particles showed a grape-like structure with high porosity, which can contribute to good reconstitution properties. the CI and HR values of agglomerated WPI-fortified SMP particles exhibited very good flowability (CI: <15) and low cohesiveness (HR: <1.2) compared to raw WPI-fortified SMP particles. In addition, agglomerated WPI-fortified SMP particles exhibited the faster wetting time than the instant criterion (<20 s). However, the level of agglomeration decreased with increasing WPI ratio, resulting in a slight decrease in particle size and wettability. therefore, it can be recommended that the SMP with a high ratio of WPI (SMP7/WPI3) requires the longer agglomeration time in the fluidized bed process. However, the extension of agglomeration time should be carefully considered from a color point of view, because the fluidized bed process can decease the CIE L* and increase the CIE b* due to the Maillard reaction. Although WPI enrichment can slightly suppress the agglomeration of SMP particles, the fluidized bed agglomeration process can effectively improve the physical properties such as particle size distribution, flowability, and wettability of WPI-fortified SMP particles. In addition, the rehydrated milk beverage with the agglomerated SMP7/WPI3 sample (60 g in 180 mL water) can be expected to provide approximately 19.3 g of whey protein and a total of 31.7 g of proteins. therefore, these results may be useful in formulating protein-fortified dairy powders with better instant property.